Part 3: How Small Manufacturers can approach Physical AI and Digital Transformation
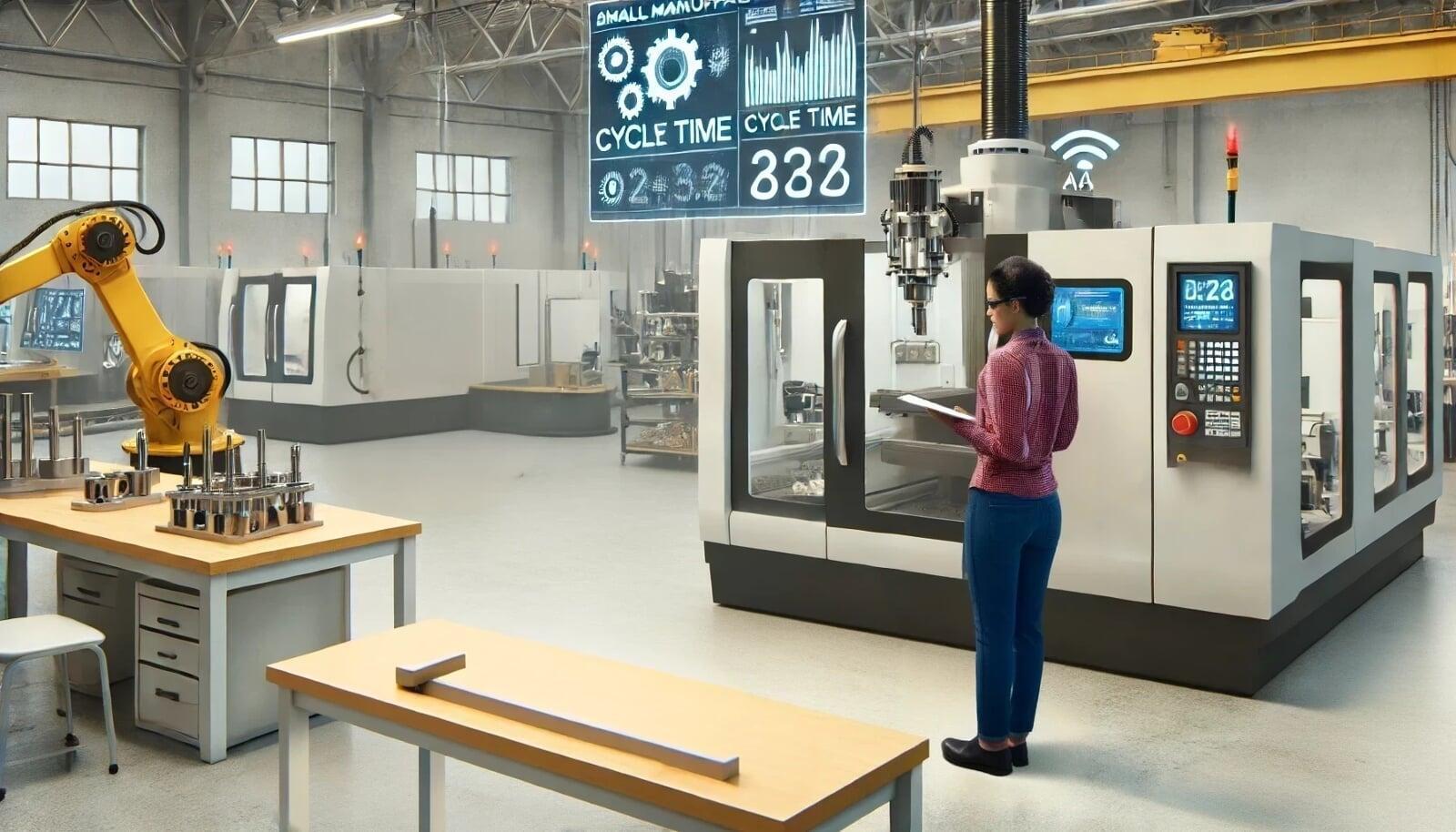
Small manufacturers don’t need full-scale automation to compete in Industry 4.0. Instead, strategic AI-assisted decision-making, workforce knowledge capture, and targeted automation can significantly improve efficiency and profitability without overwhelming upfront investments. But where do you start? And how do you ensure real ROI within 3-6 months before making further investments?
This sample roadmap breaks down the step-by-step process for a $20-80M revenue component manufacturing firm looking to modernize operations without disrupting daily workflows, while skilling their people and adding manufacturing capabilities.
📌 Step 1: Start with a SIRI Assessment & Cybersecurity Strategy(0-6 months)
🔹 Why? Small manufacturers often struggle with digital adoption because they lack a clear roadmap and secure IT infrastructure.
✅ SIRI (Smart Industry Readiness Index) Assessment helps identify the most high-impact digital transformation priorities.
✅ Cybersecurity & Role-Based Access ensure that as digital systems grow, data remains protected from cyber threats and internal misuse.
✅ Quick digital upgrades (ERP, IoT tracking, digital logs) replace inefficient manual scheduling, inventory tracking, and job costing.
📌 Step 2: Scale Digital Workflows & Introduce AI-Assisted Insights(6-12 months)
🔹 Why? Many shopfloor processes still rely on institutional knowledge and manual decision-making, making it difficult to scale.
✅ AI-driven scheduling & predictive maintenance optimize machine uptime and reduce operator workload.
✅ Supplier & customer digital integration streamlines ordering, material tracking, and order status updates.
✅ AI-powered quality control reduces defect rates and minimizes manual inspection needs.
📌 Step 3: Introduce Semi-Automated Workstations & AI-Assisted Job Planning(12-18 months)
🔹 Why? The real challenge in small manufacturing is that operations depend heavily on experienced employees. Capturing their expertise digitally and integrating semi-automated tools helps new employees adapt faster while improving efficiency.
✅ Semi-automated workstations support operators in repetitive tasks, freeing them up for higher-value operations.
✅ AI-assisted job quoting & profitability analysis ensures accurate cycle time and cost estimates, focusing on final validation.
✅ Knowledge Management System (KMS) captures machinists' expertise, automating setup, troubleshooting, and production processes.
Why This Approach Works for Small Manufacturers?
🔹 It’s phased for ROI—see real improvements before making further investments.
🔹 It balances human expertise with automation—keeping employees engaged, augmenting capabilities.
🔹 It ensures security & control—safeguarding business data while digitizing processes.
🔹 It improves efficiency & profitability—driving sustainable growth without massive upfront costs.
Step by Step guide for a small manufacturer considering digital transformation
For small manufacturers machining engineered metal parts, digital transformation and AI adoption must be practical, cost-effective, and phased for quick ROI. Large-scale automation is not feasible in the short term, but leveraging data and AI for decision-making, capturing workforce knowledge, and optimizing processes can drive efficiency and profitability with smaller investments.
This roadmap is structured to deliver measurable improvements within 3-6 months before committing to larger AI-driven changes. The Smart Industry Readiness Index (SIRI) Assessment ensures the manufacturer focuses on the right digital transformation steps without wasted costs or complexity.
Note: This is one possible SIRI prioritization roadmap for a small manufacturer (producing metal components using CNC machines, owner driven for 30+ years, revenue $20-80M range, facing common challenges such as delayed delivery, increased quality compliance, aging workforce, eroding profitability)
🔹 Phase 1 (0-6 Months): Laying the Digital Foundation & Capturing Real-Time Data
💡 Focus: Conduct a SIRI assessment, implement foundational digital tools, and train employees on digital workflows.
🔹Outcome: Clear, structured priorities to avoid wasting money on ineffective digital initiatives.
1. Conduct a Smart Industry Readiness Index (SIRI) Assessment
📌 Goal: Identify gaps, set clear priorities, and create a structured roadmap.
✅ Engage a Certified SIRI Assessor
Conduct a structured assessment using the SIRI framework to measure maturity across:
Process: Automation, shopfloor connectivity, supply chain integration, Analytics.
Technology: Tools, IoT, AI, predictive maintenance, cybersecurity.
Organization: Workforce skills, leadership, governance, change management.
✅ Deliverables of SIRI Assessment:
Benchmark the manufacturer’s digital readiness against industry standards.
Identify priority projects that offer the quickest ROI.
Set baseline KPIs for tracking progress.
✅ Baseline Metrics to Track ROI: Example
Current vs. target inventory accuracy (Improve from 75% to 90%).
Cycle time tracking efficiency (Manual vs. digital logs).
Machine utilization rates & downtime reduction.
Order processing time (Manual vs. AI-assisted scheduling).
2. Cybersecurity Assessment & Role-Based Access Implementation
📌 Goal: Ensure data protection and secure digital transformation implementation.
✅ Conduct a Cybersecurity Assessment (Aligned with SIRI Findings)
Identify vulnerabilities in existing IT infrastructure.
Evaluate risks related to shopfloor connectivity, external integrations, and supplier data sharing.
Define risk mitigation strategies before implementing new digital tools.
✅ Implement Role-Based Access Control (RBAC)
Restrict sensitive data access based on job roles.
Implement multi-factor authentication (MFA) for financial and operational systems.
Establish user-level access permissions for ERP and machine monitoring tools.
✅ Owner’s Benefit:
Ensures secure digital adoption and reduces cyber threats.
Protects sensitive financial, customer, and production data.
Strengthens internal governance & compliance.
3. Quick Tech Setup: Implementing Low-Cost Digital Tools
📌 Goal: Replace manual processes with digital tools based on SIRI recommendations.
✅ Digitize Work Orders & Inventory Management
Replace paper/manual processes with ERP software or cloud-based tools.
Barcode scanners to receive, track inventory instead of manual entries.
✅ Install IoT Sensors for Real-Time Machine Tracking
Connect CNC machines to IoT devices.
Monitor cycle time, downtime, and efficiency in real-time.
Understand utilization, availability for new opportunities
4. Workforce Upskilling: Ensuring Smooth Adoption of Digital Tools
📌 Goal: Reduce fear of technology and improve digital literacy for shopfloor staff.
✅ Customized Training Plan Based on SIRI Assessment
Operators log cycle time digitally instead of manual logs.
Finance/admin staff transition to data-driven job costing.
✅ Hiring Considerations: No need for a full IT team yet. Instead,
Engage a consultant for 3-6 months of digital coaching.
Train an internal champion to manage digital workflows.
🔹 Phase 2 (6-12 Months): Scaling Digital Workflows & Decision Making
💡 Focus: AI-driven scheduling, supplier/customer integration, predictive maintenance.
🔹Outcome: Increase capacity of the people through tools and improve data-driven decision making.
5. Digital Scheduling Tools & Shopfloor Optimization
📌 Goal: Improve on-time delivery by optimizing work order sequencing.
✅ Deploy AI-based job scheduling software
Optimizes work order sequencing based on real-time machine data.
Reduces delays and improves resource utilization.
6. Automate Quality Control & Improve Delivery Estimation
📌 Goal: Reduce defect rates & improve visibility across the supply chain.
✅ AI-Based Vision Inspection
Replaces manual sample inspections with automated quality control.
Targets 30% faster defect detection & lower rework costs.
✅ Real-Time Analysis of Material Availability
Using digital tools that connect customer orders, forecasts and ERP, AI predicts material shortages & auto-suggests supplier orders to planner.
🔹 Phase 3 (12-18 Months): AI-Assisted Job Planning & Shopfloor Automation
💡 Focus: Digitize job planning, capture machinist expertise, and enable targeted shopfloor automation.
🔹Outcome: Improve ability of your staff to attract, onboard and train new hires and set them up for success.
7. Capturing Knowledge from Experienced Staff & Creating AI-Driven Work Instructions
📌 Goal: Prevent knowledge loss & make hiring/training easier.
✅ Develop a Knowledge Management System (KMS)
Digitally document how senior machinists estimate jobs & troubleshoot issues and use these for training next-gen talent
Use AI to create standardized decision trees for CNC operations to support new hires
AI-powered guides for new hires based on real production data.
8. AI-Assisted Job Quoting & Profitability Estimation
📌 Goal: Automate job feasibility & pricing decisions.
✅ Automated Drawing Analysis & Job Feasibility Tool
AI scans customer drawings to estimate:
Cycle time, operations needed, & material requirements.
Profitability per job (using real-time cost tracking).
✅ AI-Based Quoting Dashboard
Auto-generates cost estimates within minutes.
Suggests optimized production routing.
9. Introduce Semi-Automated Workstations to Support Operators
📌 Goal: Assist operators in handling repetitive tasks, freeing them up for higher-value operations.
✅ Semi-Automated CNC Workstations
Equip workstations with automated material handling to reduce manual lifting & positioning.
Use auto-tool changers & presetting systems to minimize setup time.
Introduce guided work instructions on digital interfaces at machines.
✅ Collaborative Robots for Support Tasks
Deploy robotic arms for loading/unloading CNC machines.
Use AI-assisted welding, polishing, or deburring tools to reduce operator workload.
✅ Owner’s Benefit:
Operators focus on precision machining instead of repetitive tasks.
30% faster machine setup & changeover.
Higher worker retention by reducing physically strenuous tasks.
Bottom Line: A Realistic, Phased and Need-based Approach to Digital Transformation for Small Manufacturers
Digital transformation isn’t just for large-scale factories—it’s an opportunity for small manufacturers to improve efficiency, reduce costs, and future-proof their business. But the key to success isn’t overhauling everything at once—it’s about starting small, prioritizing quick wins, and scaling based on real impact.