Part 1: What’s the Difference Between Physical AI and Digital Twins in Manufacturing?
Nvidia recently made its announcement about Cosmos and its application to Physical AI. We reflected on its relation to Digital Twins in manufacturing, which are impactful in the product, process and performance optimization and adjustment. we will explore it in three parts over the next few days:
- Part 1: The difference between Physical AI and Digital Twins
- Part 2: Technological advancements needed for Physical AI adoption in Manufacturing
- Part 3: Making physical AI and digital twins accessible to Small and Mid-Scale Manufacturers
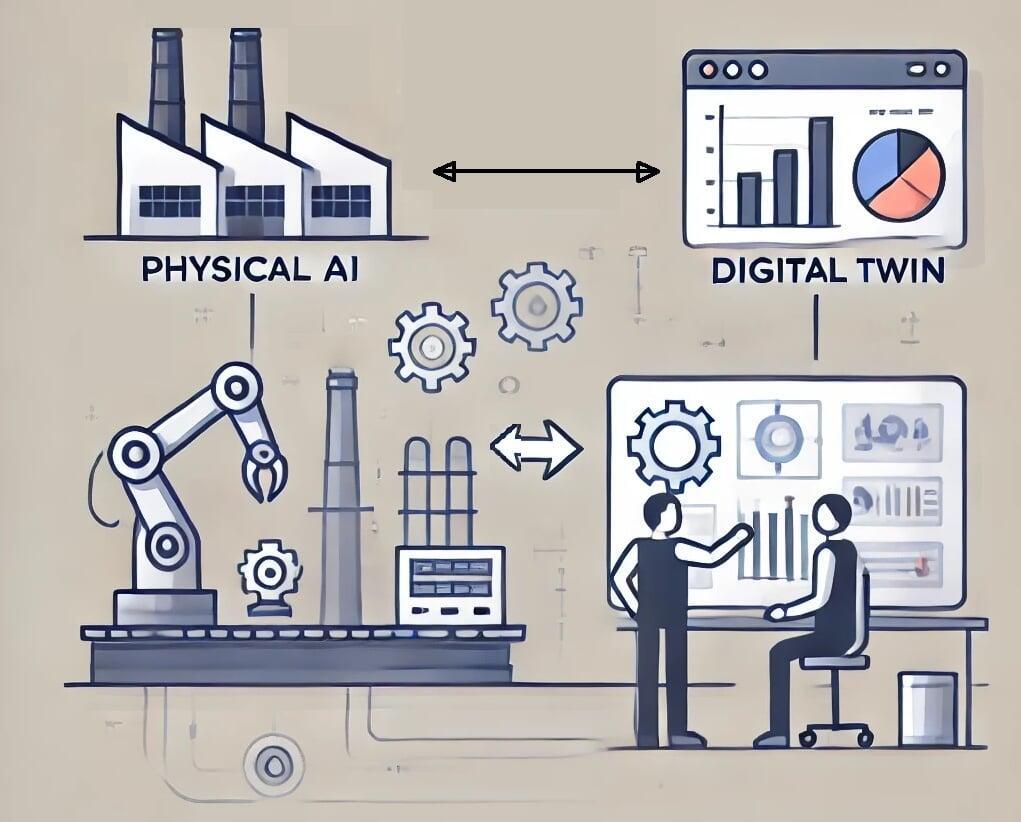
In manufacturing, an exciting technology is making waves: Physical AI. While physical AI and digital twins often work hand-in-hand, they’re not the same thing. If you’re wondering how they differ, here’s a quick breakdown to clear things up.
What is Physical AI?
Think of Physical AI as smart systems that operate in the real world. It’s about robots, machines, and even materials that can adapt and act autonomously. For example, a robotic arm equipped with AI can adjust its grip on the fly, making it perfect for handling delicate or variable-sized objects, say handling a rubber washer vs. a metal plate during assembly. Physical AI systems are all about acting on real time intelligence received from the physical systems.
What is a Digital Twin?
On the flip side, Digital Twins are virtual replicas of physical assets or processes or performance. They typically do not act in the physical world but instead create a digital space of your products or factory where you can simulate, analyze, and optimize operations. For instance, a Digital Twin of a factory floor can model production scenarios, predict machine failures, and test material flows/ bottlenecks—all without interrupting the actual process.
So, What’s the Difference?
Here’s the key: Physical AI gets things done in the real world, while Digital Twins help you figure out the best way to get things done.
- Physical AI systems are designed to act autonomously and adapt in real time.
- Digital Twins simulate and analyze, offering insights to optimize the physical systems they represent.
In terms of technologies:
· Physical AI combines robotics, AI algorithms, sensors, actuators, field devices and increasingly, bio-inspired materials to create intelligent physical systems.
· Digital Twin relies on IoT sensors, data analytics, machine learning, simulation software, and cloud/edge computing to virtualize and predict physical system behaviors.
So snstead of transforming into one another, Physical AI and Digital Twins collaborate in a feedback loop:
- From Physical AI to Digital Twin: Real-time data from Physical AI systems update the Digital Twin to ensure the virtual model reflects the current state of the physical system.
- From Digital Twin to Physical AI: The Digital Twin’s simulations and predictions optimize the operations of the Physical AI system, improving efficiency, performance, and reliability.
They serve different stages of the manufacturing lifecycle, and their strength lies in their collaboration rather than any attempt to merge or replace one another.
Better Together
Even though they’re different, Physical AI and Digital Twins can work together. Data from Physical AI systems can update Digital Twins for accurate modeling and response. At the same time, insights from Digital Twins can tweak and improve Physical AI systems and the hardware design. By combining their strengths, these technologies can revolutionize manufacturing, making it smarter, faster, and more efficient. Physical AI is still in its early stages, and our understanding will grow as we apply it across industries. I am looking forward to explore and learn a lot more!