Series: Designing Intelligence – The Strategic Use of Digital Twins in OEM Manufacturing
Introduction to the Series
In this three-part series, we explore how digital twins can help OEM manufacturers move from reactive decision-making to intelligent, data-driven operations. From early-stage design to procurement strategy and workforce enablement, digital twins—when implemented beyond surface-level 3D models—can serve as an integrated, cross-functional foundation for growth and resilience. The discussion is focused towards OEM in industrial engineered goods segments.
This three-part series explores how digital twins can serve as a force multiplier across:
Part 1: Design agility and engineering integration
Part 2: Operational Digital Twins for shopfloor and supply chain management
Part 3: Connected worker enablement and training scalability
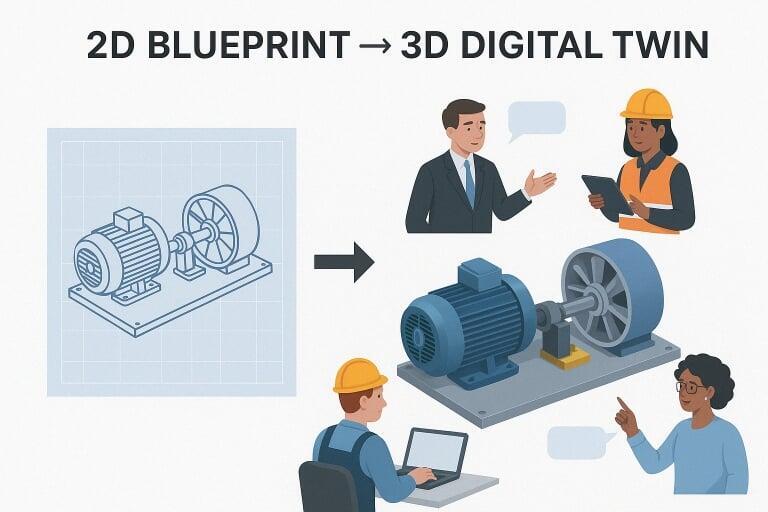
Part 1: Designing for Intelligence – How Digital Twins Transform OEM Engineering
OEM manufacturers operate under tight margins and even tighter schedules. They are expected to deliver high-performance, application specific tolerance equipment, new capabilities with short lead times—often across multiple sectors. Yet, many continue to rely on fragmented digital tools, tribal knowledge, and ad hoc processes in their design workflows.
Digital twins offer a new way forward. When treated as intelligent, simulation-ready platforms, they can significantly reduce time-to-market, improve first-time-right builds, and make engineering teams more adaptive in the face of constant change.The Common Design Inefficiencies at OEMs
From personal experience managing OEM manufacturing operations, I have observed a few recurring challenges:
Minimal design reuse leading to excessive SKU proliferation.
Engineers working in disciplinary silos—mechanical, electrical, and controls rarely collaborate early.
Under utilization of engineering tools: many OEMs design teams are unaware of advanced capabilities like automated fitment analysis, harness layout optimization, or physics-based simulations built into existing tools.
Inadequate annotation of CAD files, making search, reuse, and referencing difficult.
PLC programming begins post-build, leading to delays in commissioning and late stage reworks.
Drawings are seen as static deliverables, not dynamic digital assets that can power downstream workflows.
💡 The Digital Twin as a Multi-Domain Design Platform
OEMs often mistake digital twins for 3D visualizations. In reality, a digital twin—when properly developed—is a multi-disciplinary, simulation-ready asset that connects design intent across engineering, manufacturing, service, and even sales. It is a living, connected, multi-domain model. It integrates mechanical, electrical, and control logic to answer “what-if” questions before physical execution. This unlocks major value in areas OEMs often struggle with:
Early detection of fitment and clash issues across mechanical and electrical systems.
Simulation of control logic, enabling virtual commissioning and early bug resolution.
Cable/harness planning, factoring in motion, serviceability, and compliance zones.
Cross-functional collaboration, aligning design, manufacturing, and field teams with a shared digital source of truth.
Model and validate IoT capabilities based on field feedback (e.g., alarms, maintenance triggers, sensor placements).
Design impact modeling—allowing changes to alternate components to be evaluated in real time.
At many OEMs, adapting designs for alternate parts is a manual, trial-based process that depends heavily on the engineers' and technicians' recollection of past instances. A digital twin can surface cascading dependencies, alert affected sub-assemblies, and simulate behavior changes—saving time, cost, and errors.
Key Impact Areas
🔹 Design Reuse & Modularity
Well-structured digital twins allow for validated design modules to be reused across product lines. This cuts down design cycles, accelerates sourcing, and supports scalable customization. I see new AI tools coming to facilitate natural language input for design generation, annotation and search.
🔹 Underutilized Tools
Most OEMs are unaware of the full depth of capabilities in their CAD and simulation environments. By working with engineering tool vendors to map desired capabilities (e.g., motion analysis, embedded system testing, ECAD-MCAD integration) to available modules, companies can unlock immediate value. Vendors often offer training, industry examples, and simulation templates that go unused due to lack of awareness or cross-functional planning.
🔹 Component Substitution & Change Management
When alternate components must be selected—due to supply chain constraints or obsolescence—OEMs often rely on engineers’ past experience to assess the downstream impact. A well-built digital twin can automate this process, identifying affected assemblies, control logic dependencies, or spatial constraints. This enables faster, safer decision-making under pressure.
🔹 Simulate Before You Build
Digital twins allow engineers to run simulations for motion paths, safety interlocks, cycle times, MTBF studies—before physical component is even procured. Virtual commissioning reduces risks and shortens installation time.
🔹 Designing with Real-World Input
IoT feedback loops from field service and customer usage can inform design decisions—identifying common failure points, underperforming components, or usability issues. This input, when modeled in the twin, helps future-proof products.
What OEMs Must Do Differently
To realize this value, OEMs must evolve foundational practices:
✅ 1. Strategically Define the Capabilities Needed in Design
Identify the product characteristics and lifecycle insights you want to capture, collaborate, simulate. Then work backward with tool vendors to configure your stack accordingly.
Metadata, annotations for design reuse
Motion and fitment
Controls and PLC logic
IoT behavior and fault triggers
Virtual commissioning
✅ 2. Partner with Tool Vendors as Strategic Allies
Don’t treat them as sales reps—engage them as capability partners. Ask:
What features are underused in our environment?
What training can accelerate our simulation maturity?
What are other industries doing that we can adapt?
✅ 3. Simulate First, Build Second
Invest in virtual environments that allow product design, testing, and validation across disciplines before procurement or build. This must become the new normal—not an exception.
Conclusion: Designing with Intelligence
OEM manufacturers can no longer afford to treat design engineering as a siloed function. Design must now serve sales, procurement, manufacturing, and service simultaneously. This is only possible with a well-developed, living digital twin that brings transparency, traceability, and foresight into the process.
👉 Next in the Series: How Digital Twins Create Operational Digital Twins in OEM Manufacturing
We’ll explore how design-stage digital twins support better BOM planning, cost estimation, sourcing flexibility, and operational execution.