Augmenting Human Potential: Designing the Future with Digital Tools
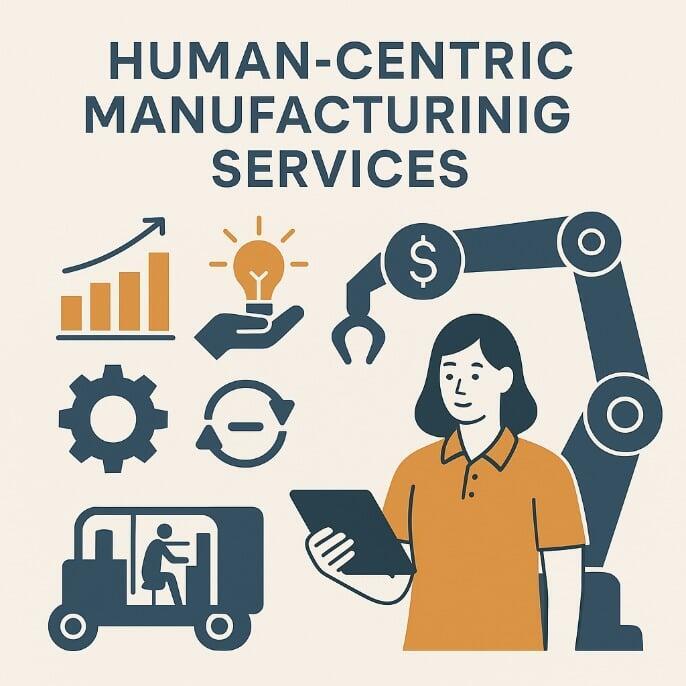
Summary
In this article, Arthi Sairaman shares insights from her Stealth Summit 2025 Lightning Talk on how small and mid-sized manufacturers can adopt a human-centered approach to digital transformation. She explores how tools like Connected Worker platforms, Digital Twins, and Process Blueprinting can augment human potential, improve decision-making, and enable scalable, resilient operations—without overwhelming teams or disrupting business continuity.
In today’s rapidly evolving manufacturing landscape, the role of technology is no longer just to automate tasks—it is to augment human potential. That was the core message of my Lightning Talk at the Stealth Summit 2025, where I explored how small and mid-sized manufacturers can thrive by embracing digital tools that enhance—not overwhelm—their people.
The Opportunity in the Chaos
Manufacturing in the U.S. is at an inflection point. The reshoring is creating long term opportunities and exposing unresolved vulnerabilities. Small and mid-sized manufacturers, who form the backbone of our industrial base, are under immense pressure. They face:
Acute labor shortages and succession issues
A deluge of digital transformation and cybersecurity demands
A perception that automation is unaffordable or ill-suited for their size
Start with a Manufacturing Tech Health Check
Similar to a financial health check, manufacturers must assess their digital fitness- what I call Manufacturing Technology Balance Sheet. Tools like the Smart Industry Readiness Index (SIRI) provide a structured framework to uncover:
Technology debt built over years of tribal knowledge, paper-based workflows, and siloed systems
Efficiency leaks from outdated tools and disconnected processes
Misaligned priorities, where symptoms are mistaken for root causes
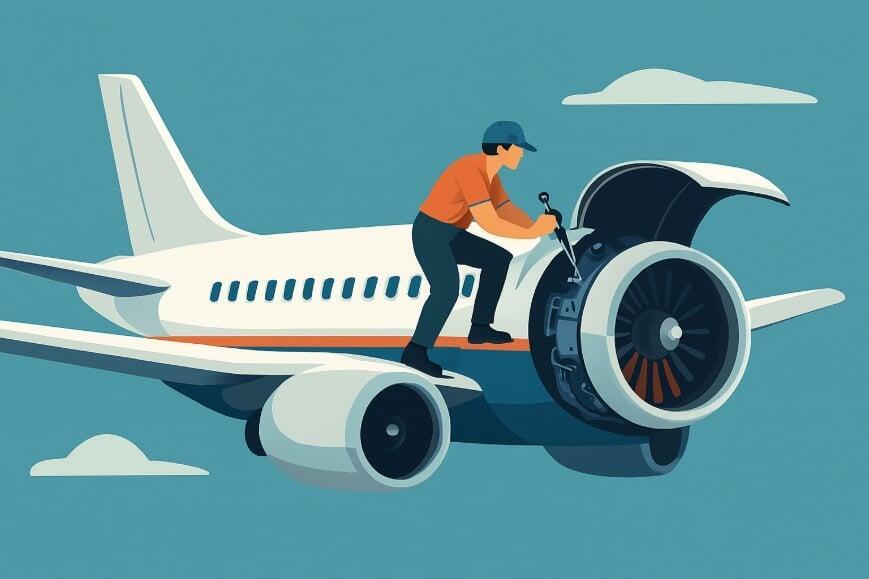
Changing the Engine While Flying the Plane
Digital transformation occurs while the business continues running. This is akin to changing the engine while flying the plane—and it requires precision, clarity, and a phased approach.
Here are three ideas to build capability while minimizing disruption and enabling adoption:
1. Connected Worker Platforms: People first
Today’s workforce learns and operates differently. We must replace binders and verbal instruction with digital, role-based, context-aware tools. Connected Worker Platforms aggregate static documents, SOPs, reports, and drawings, and deliver dynamic content via mobile and AR devices—accelerating onboarding, improving safety, and developing human capacity.
2. Process Blueprinting for System-Driven Actions
Many shopfloor activities are still triggered manually, which is unsustainable. To start with, digitally blueprinting and systematizing critical operations enables information flow across functions, triggers cross-functional processes, supports exception-based decision-making, and reduces waste from waiting and miscommunication. I can tell stories when the absence of one person in the manufacturing value chain introduced multi-day delays and disruption.
3. Digital Twins: Utilize this asset.
A digital twin is more than a virtual replica of hardware, process or supply chain. When designed well, it becomes a shared intelligence layer across the enterprise—from sales and planning to production, service, and even the customer. Digital twins allow for:
Scenario testing
Cost and time reduction
Decision support across product lifecycle
When tied to real-time data and operations, digital twins become assets that unlock new business models, such as outcome-based services or predictive maintenance offerings.
Designing Services That Develop Human Capital
The future of manufacturing isn’t just digital—it is human-centered. Many transformation projects will be brownfield, requiring integration with legacy systems and human adaptability. Success depends on designing solutions with the following principles:
Start small, deliver value, scale pragmatically
Small, outcome-driven implementations build confidence and minimize risk.
Adopt flexible, service-based models
Manufacturers are shifting from capital investment to robots and software as a service, giving them agility without long-term lock-in.Embed learning in the flow of work
Implementation providers must prioritize creation of a knowledge base, skills training, and change management. Connected worker tools and digital learning environments reduce dependency on informal knowledge transfer.Use data analytics to elevate people, not just performance
For the near future, employees remain at the center of decisions. Dashboards must show how employee interventions—setup changes, quality catches, problem-solving—drive productivity and improvement. This creates visibility, encourages innovation, and builds a strong talent pipeline.
Final Thought
The future of manufacturing is about human capital development. It is about designing systems that amplify their capabilities, scale their strengths, and unlock innovation.
By embracing connected platforms, digital twins, and human-first design, we can create a resilient and inclusive manufacturing ecosystem—one where technology empowers talent.